Ti -6Al-4V(以下簡稱TC4)是美國于1945年.開發(fā)出的一種兩相鈦合金,由于其良好的綜合性能及工藝特性,成為鈦工業(yè)中的王牌合金,被廣泛的應用于化工、電力、航空航天、體育器械等領域。迄今為止,雖然TC4已經(jīng)問世了70多年的時間,但是由于人們對于材料設計概念的變化,以及新技術、新應用領域的開發(fā),TC4鈦合金仍然是當今鈦合金研究中的熱點合金。目前成本問題是限制鈦合金應用的一個重要因素,受此影響,低成本的合金化設計以及近凈成型技術尤其是增材制造技術的開發(fā)是目前鈦合金領域一個非常關注的話題。本文簡要介紹了近些年來圍繞著TC4鈦合金的成分改進、近凈成型工藝開發(fā)進展。
1、成分設計與開發(fā)
合金的成分從根本上決定了合金的性能,隨著現(xiàn)今對于材料性能要求的日益提高,以及材料設計概念的改變,人們對于TC4合金進行了不同程度的成分優(yōu)化再設計,以期滿足不同的需求。針對TC4的成分優(yōu)化再設計有很多,例如早期的TIMETAL62S(Ti- 6Al - 2Fe - 0.1Si)、Ti8LC(Ti - Al - Fe -Mo)、Ti12LC(Ti- Al- Fe- Mo)等(3.4。近些年來也相繼發(fā)展了TIMETAL CI4(Ti-5Al-3V - 0. 6Fe -0. 10)、 ATI 425(Ti -4Al -2.5V - 1.5Fe -0.250)、Ti575(Ti-5.3Al-7.7V -0.5Si)、Ti - 54M(Ti- 5Al-4V -0.75Mo-0.5Fe)、Ti407(Ti -0. 85Al - 3.7V-0.25Fe -0.25Si)等一系列TC4改型鈦合金。針對TC4改型的目的主要有兩個,一個是出于性能考慮,尤其是其動態(tài)力學性能。例如Ti575合金,相比于TC4,該合金降低了Al當量,提高了Mo當量,并加入了少量的Si來提高合金的強度。其抗拉強度與屈服強度均高于TC4,并且在抗拉強度1 200 MPa時,延伸率可達到10.5%,比強度比TC4高出8%.并且相比于TC4合金,該合金具有更好的疲勞性能和可鍛性。針對TC4改型的另一個目的在于降低成本。TIMETAL CL4、ATI 425都是在TC4的基礎上降低了AI、V的含量并加人一-定量的Fe和0元素,在保證強度的同時,改善了TC4合金的冷加工性,從而降低了成本。Ti407 合金具有更低的Al當量,通過犧牲材料的強度來提高其加工性能,該合金設計目的主要是為了部分取代TC4,降低商用飛機用材的成本。Ti-54M相比于TC4,含有較低的Al當量,并且加入了少量的Mo、Fe元素來降低β轉(zhuǎn)變溫度。該合金相比于TC4,具有更好的加工性和成形性,其超塑成形能力優(yōu)于TC4材料,可以顯著降低加工成本。
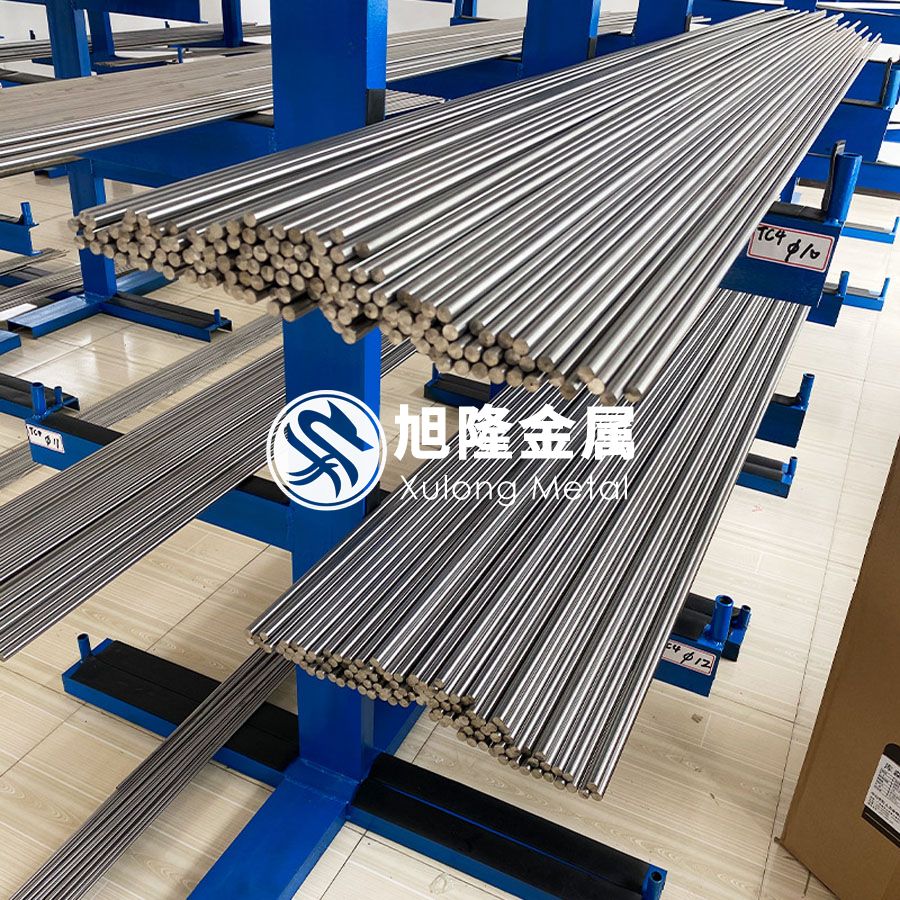
2、近凈成型工藝進展
鈦合金的成本是決定是否應用此種材料的重要因素。近凈成型技術是一種無切削或者少切削的工藝,主要包含AM(增材制造)、PM(粉末冶金)、SPF(超塑成形)以及精密鑄造技術等。由于其材料利用率高,可以有效節(jié)省加工成本,是目前鈦合金制備及加工領域的--個重要發(fā)展方向。
2.1 增材制造技術
金屬增材制造技術是目前鈦合金制備領域的一個熱點方向,各個國家也分別對其在鈦合金方面(特別是TC4)的研究與應用做了大量的工作。金屬增材制造技術是一個非常寬泛的概念,主要包含以激光立體成形技術(LSF)為代表的同步送粉(送絲)高能束(激光、電子束、電弧等)熔覆技術,和以選區(qū)激光熔化技術( SLM)為代表的粉末床成形技術[61。表1給出了LSF與SLM制造的典型TC4與鍛態(tài)拉伸性能對比7-9]。從表1可以看出,目前LSF與SLM成形的TC4零件拉伸性能均可滿足鍛態(tài)標準。對于以LSF為代表的同步送粉技術,其可以和各種傳統(tǒng)加工工藝結(jié)合,從而有效地提高致密度,因此可以獲得與退火態(tài)鍛件基本相當?shù)母咧芷谛阅堋6鴮τ赟LM工藝,由于其孔隙難以完全消除,因此會對于拉伸塑形及疲勞性能產(chǎn)生不良的影響。目前限制增材制造技術應用的因素有很多,例如高昂的粉末成本、特殊的組織形貌與織構(gòu)取向、低的疲勞性能、大的殘余應力等等。近些年來,有大量的研究試圖克服這些缺陷,例如通過引人形變的方式來弱化織構(gòu)、后續(xù)處理來改善拉伸和疲勞性能、預熱處理減小殘余應力、優(yōu)化工藝參數(shù)以獲得最小的孔隙率等等。但是,受制于增材制造特有的工藝特性,這些措施起到的效果都比較有限,而且會進一步增加成本,抵消增材制造技術的優(yōu)勢。因此,對于增材制造技術的發(fā)展,開發(fā)其專用合金勢在必行。
2.2 粉末冶金技術
傳統(tǒng)的BE(混合元素粉末冶金法)工藝制備的鈦合金往往會因為殘留的孔洞、高的氧含量以及粗大的組織,對其力學性能產(chǎn)生不利影響。通常的做法是利用粉末鍛造工藝,來減小甚至完全消除孔隙,.細化組織,但這種工藝無疑增加了成本,并且抵消了PM近凈成型的優(yōu)勢。近些年來,發(fā)展了一種基于BE的新型工藝HSPT(氫燒結(jié)和相轉(zhuǎn)變)。該工藝結(jié)合了THP(熱氫處理技術)和BE的優(yōu)點,其工藝流程圖如圖1所示3。該工藝采用可控的氫氣作為保護氣體,并利用H元素的可逆合金化作用來細化晶粒。利用該工藝制備的TC4合金致密度可以達到99%以上,并且燒結(jié)后的組織為超細晶結(jié)構(gòu),明顯提高了合金的靜態(tài)拉伸性能[4(相比于真空燒結(jié))。而且經(jīng)過簡單的熱處理工藝(無需熱加工)即可獲得類鍛態(tài)組織(雙態(tài)組織和等軸組織),且其拉伸性能明顯優(yōu)于鍛態(tài)組織。但是,目前由于人們對于(T -6Al-4V)-xH相圖缺乏進--步的理解,該相圖并沒有很好地建立起來,限制了該工藝的進一步優(yōu)化研究。而且,有文獻報道,通過該工藝制備下的TC4工件,氧含量偏高,對其性能會產(chǎn)生一定的影響。
有學者利用粉末中混人稀土元素的方式成功地緩和了PM工藝中0元素的不利影響,因此如果可以有效利用粉末中混合稀土元素的方式來改善氧的不利影響,無疑是對此種新型工藝非常有吸引力的??偠灾?由于HSPT工藝粉末無需預合金化,后續(xù)經(jīng)過簡單的熱處理即可獲得鍛態(tài)組織,可以顯著地降低PM工藝的成本,對于大批量生產(chǎn)復雜結(jié)構(gòu)的小型件是一種非常有吸引力的工藝。
2.3 超塑成形技術
超塑成形技術(SPF)是一種利用薄板材料的超塑性來成形的工藝,其優(yōu)點是可以成形復雜件,零件表面質(zhì)量好。普通的TC4材料的超塑性成型溫度在900℃以上,所需應變速率低于10-3-1,因此,其長時間的成型時間、高的成型溫度限制了其在批量生產(chǎn)方面的應用。傳統(tǒng)的解決方法是利用細化晶粒來提高材料的超塑成形能力,例如晶粒尺寸在1μm左右的TC4板材(普通的TC4板材晶粒尺寸在4~ 10μm)可以將成型溫度降低到775℃。但是這種超細晶結(jié)構(gòu)的制備無疑又增加了零件制造的成本。HP. (熱成型) +SPF是一種新型的類超塑成形工藝,其原理如圖2所示,材料先在低于超塑成形溫度下進行一-定量的預變形,隨后在一-定的氣壓下進行吹塑成形。有學者已經(jīng)利用這種工藝成功地制備出了TC4零件,并將成型溫度由原來的900C降低到了800℃,成型時間由120min降低到了16min。但是,目前關于此工藝的研究報道很少,而且對于如何有效控制預變形階段的升溫以及成形階段的氧化問題目前還沒有相應的報導。
2.4 精密鑄造技術
由于鑄造成本的降低和鈦合金鑄造質(zhì)量和產(chǎn)能的提高,鑄造鈦零配件的使用量是呈上升趨勢的,并且目前在航空航天工業(yè)中98%以上的鑄造結(jié)構(gòu)件都是采用熔模精密鑄造技術。對于高性能鈦合金大型整體精鑄件的生產(chǎn)現(xiàn)今大多數(shù)是采用金屬面層陶瓷型殼或氧化物面層陶瓷型殼澆注出來的。但是這些陶瓷模具在高溫下會與鈦溶液反應,在鑄件表面形成a層,隨后必須加以酸洗。即使采用冷坩堝感應熔煉+離心鑄造的方式可以有效降低這種富氧α層的厚度,但仍不能做到完全消除。為了避免這種現(xiàn)象以及出于規(guī)?;目紤],近些年來正在積極地研究和發(fā)展鈦合金的永久模鑄造技術。目前已經(jīng)真正獲得實用化的技術是真空壓鑄技術,但現(xiàn)階段只能批量生產(chǎn)- .些簡單形狀的鈦鑄件。限制鈦鑄造永久鑄模的主要難點在于當獲得適宜的過熱度來滿足良好充填性的同時,要使熔融鈦與鑄模之間的相互作用最小采用計算機模擬、熱等靜壓和β熱處理等技術。例如美國成功通過上述綜合工藝獲得了與鍛件靜力和疲勞性能相當?shù)拇笮蚑C4精鑄件,并已成功應用于F/A-22、V -22等軍用飛機。
3、結(jié)語
TC4鈦合金由于其優(yōu)異的綜合性能,在今天仍然是鈦工業(yè)中的主流合金。目前限制其普及化及民用化的主要問題仍然為成本問題。而且我國雖然在鈦合金。另外,為了消除傳統(tǒng)鑄造鈦合金的鑄造缺陷、改善合金的性能,常常在精鑄工藝上研究水平大體與國外接近,但是在鈦合金制備技術、加工技術、裝備水平等方面與美、俄等國家仍存在相當大的差距。例如工業(yè)生產(chǎn)中經(jīng)常存在產(chǎn)品性能不穩(wěn)定、成材率低等- -系列問題,而這些額外因素又進-步增加了鈦合金的成本。因此擬提出如下建議:
1)注重制備及加工技術的開發(fā),例如精鍛、模鍛技術、連鑄連軋技術、尤其是近凈成型技術的開發(fā)應用等等。
2)擴大計算機模擬技術在材料成型與加工領域的應用,減小工藝設計周期。
3)提高加工過程中的自動控制水平,提高產(chǎn)品的穩(wěn)定性。
4)分析研究其特殊性能,找出其有別于其它工程材料的優(yōu)勢,擴大其在新應用領域的應用。
本文作者:楊佩;康聰;李維
相關鏈接